Q&A
よくあるご質問
抵抗溶接はどの様な原理ですか。
抵抗溶接とは被溶接物を電極で加圧し、電流を流すことでジュール発熱により、加圧部分を局所的に溶融し接合するものです。
被溶接物には電極を介して電流を流しますが、電極には銅合金等を使用するため、電極は被溶接物に比べて抵抗が低く、相対的に接合部の温度上昇が大きくなり、被溶接物だけが溶接されます。
接合部に集中的に熱を発生させるため、アーク溶接などに比べて一般的に短時間で熱歪みの少ない溶接が可能です。
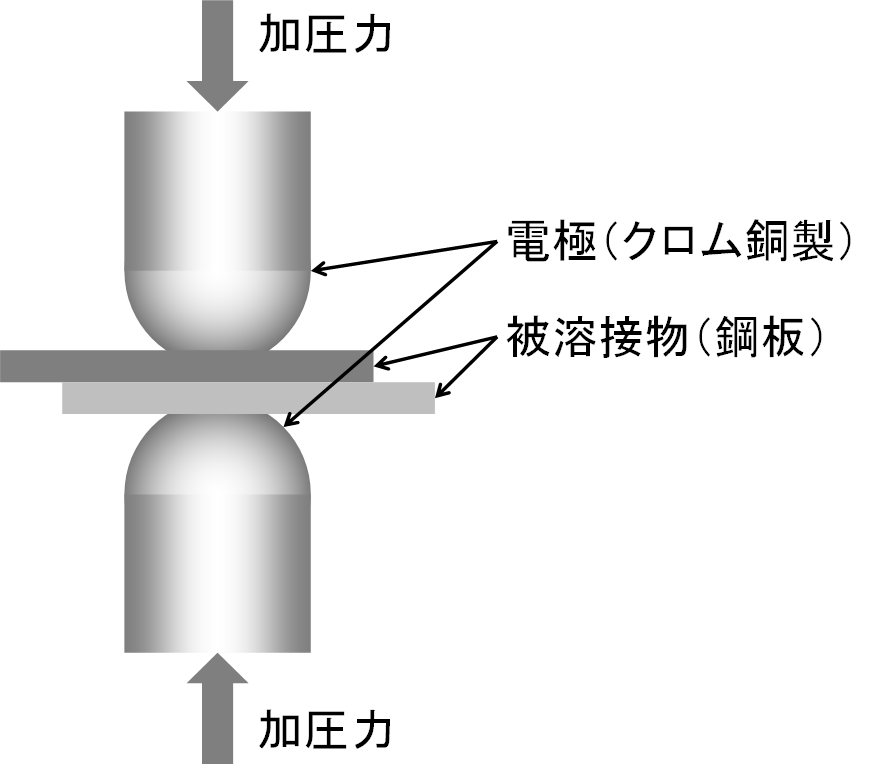
スポット溶接の概略図
抵抗溶接にはどのような種類がありますか。
抵抗溶接は大きく分けて重ね抵抗溶接と突合せ抵抗溶接に分類されます。
重ね抵抗溶接はスポット溶接、プロジェクション溶接、シーム溶接に、突合せ抵抗溶接はバット溶接、フラッシュ溶接に分類されます。
スポット溶接とは一対の電極で複数枚の板を挟み、大電流を流すことで板の重ね部を溶かし、ナゲットを作り溶接する方法です。
自動車のボデー組立などに多用されています。
プロジェクション溶接とは一方の被溶接物に突起(プロジェクション)を設けることで相手部材と溶接する方法です。
自動車のボデー部品等にナットを溶接する際に多く使用されています。
シーム溶接とは原理的にはスポット溶接と同じですが、電極を回転可能な円板状とし連続で溶接する方法です。
自動車のガソリンタンクやドラム缶、灯油の燃料タンクなど気密を要する溶接に多く使用されています。
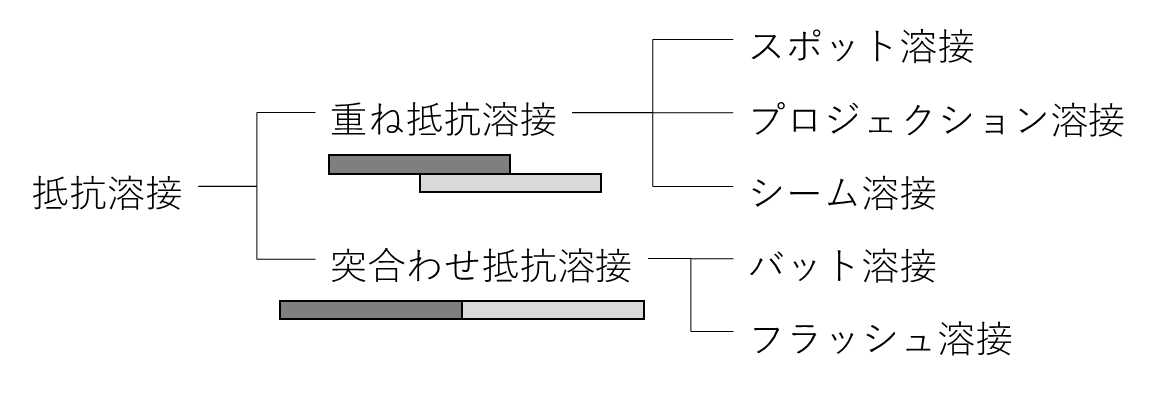
抵抗溶接の分類
溶接する際に重要な条件は何ですか。
抵抗溶接の三大条件と呼ばれるのは電極加圧力、溶接電流、通電時間です。適切な溶接条件を設定することで、作業者のスキルに因らず安定した溶接が可能です。
スポット溶接やシーム溶接の場合、三大条件の他に電極先端形状が重要になります。これは電極と被溶接物との接触面積を小さくすることで、溶接する部分の電流密度を高めて溶接するためです。この電極形状を含めて四大条件と呼ばれることもあります。
プロジェクション溶接の場合、三大条件の他に突起形状や電極の平行度が重要になります。これは突起により電流密度を高めて溶接するためです。
以上の条件の組み合わせにより溶接の良否が左右されます。
溶接のナゲットとは何ですか。
スポット溶接やシーム溶接をすると、接合部が溶融・凝固しますが、この溶融・凝固した部分をナゲットと呼びます。
ナゲットは溶接部分を切断し腐食することで観察することが出来ます。図のハッチング部がナゲット、その周辺部はHAZと呼ばれる熱影響部です。
スポット溶接などの品質基準として「ナゲット径5√t以上」等と表現することが有ります。(tは板厚を示します。)
プロジェクション溶接では一般的にナゲットは出来ませんが、プレスにより打ち出した突起(エンボス突起)の場合などに、ナゲットが出来る場合があります。

スポット溶接部断面図
溶接実験を依頼することができますか。
ご依頼の実験内容によりますので、先ずはその内容について弊社担当営業もしくはお問い合わせフォームにてご相談ください。
尚、弊社には以下の通り多くの実験装置(設備)を保有しています。
・スポット溶接機:単相交流式、直流INV式、交流INV式、三相整流式、コンデンサ式
・プロジェクション溶接機:単相交流式、直流INV式、交流INV式、三相整流式、コンデンサ式、インバータ制御コンデンサ式
・シーム溶接機:単相交流式、直流INV式、交流INV式
その他にもポータブルシャーウェルダ、熱かしめ装置、抵抗加熱装置、レーザ溶接設備も御座います。
また、評価設備として万能試験機(500kN)、断面マクロ試験設備、デジタルマイクロスコープ(×20~×200)、エリクセン試験機、ダイヤル型手動式トルクレンチなどを保有しております。
溶接実験を依頼する際に必要な情報は何ですか。
被溶接物の形状・材質などがわかる図面など、ご要求される溶接品質の情報が必要です。
更に、生産タクトなどの情報を戴けますと、実際の溶接機の構想を念頭に実験を進められます。
スポット溶接する際の溶接条件の決め方を教えてください。
先ず溶接条件表などを参考に、加圧力、通電時間、電極先端形状を仮に決めます。
その条件で電流を低い値から徐々に上昇させ、必要なナゲット径が得られる電流値と散りが発生する電流値を確認します。その間が適正電流範囲であり、その中間程度を溶接条件として採用します。より厳密に溶接条件を決定する場合には図の様なウエルドローブを作成して決定します。
亜鉛めっき鋼板の場合は、一般的に高加圧力、長時間通電、高電流になります。また、めっきが電極に付着し易いため、電極ドレスを頻繁にする必要があります。
高張力鋼板(ハイテン材)は一般的に高加圧力、長時間通電、低電流になります。また、加圧力だけで板隙を無くすことが困難な場合は、2回通電や3回通電が有効な場合もあります。なお、ハイテン材は溶接時に焼きが入りますが、焼き戻し電流(テンパ電流)で材料の延性を増すことが出来ます。
ステンレス鋼の場合は固有抵抗が高いため低い電流で溶接が可能です。但し、マルテンサイト系の場合には焼きが入りますので、ハイテン材と同様に焼き戻し電流を流す必要が有ります。
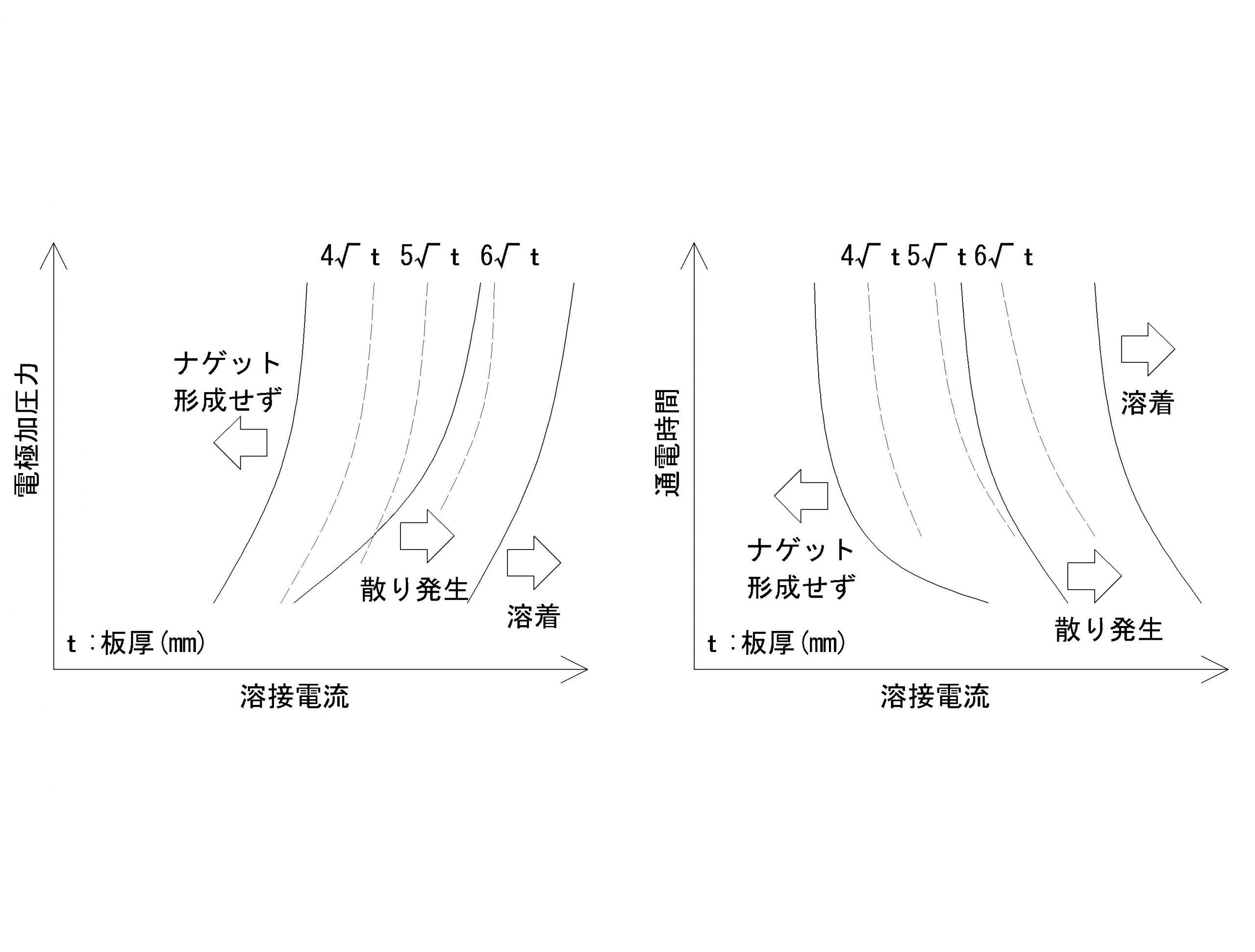
ウエルドローブ
様々な種類の電源が有りますが、何が違うのですか。
単相交流式は最も構造がシンプルで安価なことから定置式の溶接機では一般的に採用され、ほとんどの被溶接物を溶接可能です。
直流インバータ式はサーボスポットガンの様に、軽量化が求められる場合に多く採用され、商用周波数の20倍以上の周波数に変換することで、トランスのコアを小さくでき、溶接トランスの小型・軽量化が可能となります。しかし、周波数が高くなると二次電流が流れ難くなるため、トランスの二次側に整流器を配置し直流化して使用します。また、薄板の場合に散りが出難い事や、通電時間の設定が交流式のサイクル単位に対し、ミリ秒単位で細かく設定出来ることから採用される場合もあります。
コンデンサ式の場合は、一旦コンデンサバンクに充電して、溶接時に一気に放電するので、受電容量を小さくすることができます。そのため電源事情が悪い場合や、大型のプロジェクション溶接機の様に大電流が必要な場合に採用されています。また、他の電源と比べ短時間大電流通電が可能で、周囲への熱影響が少ないために、溶接後の変形や残留応力が少なくなる特長があります。現在ではホットプレス(ホットスタンプ)材等にナットやボルトをプロジェクション溶接する際にも使用されることが増えています。
その他、交流インバータ式、単相整流式、三相整流式、三相低周波式などの電源があり、被溶接物の要求条件や諸条件を考慮し選択します。
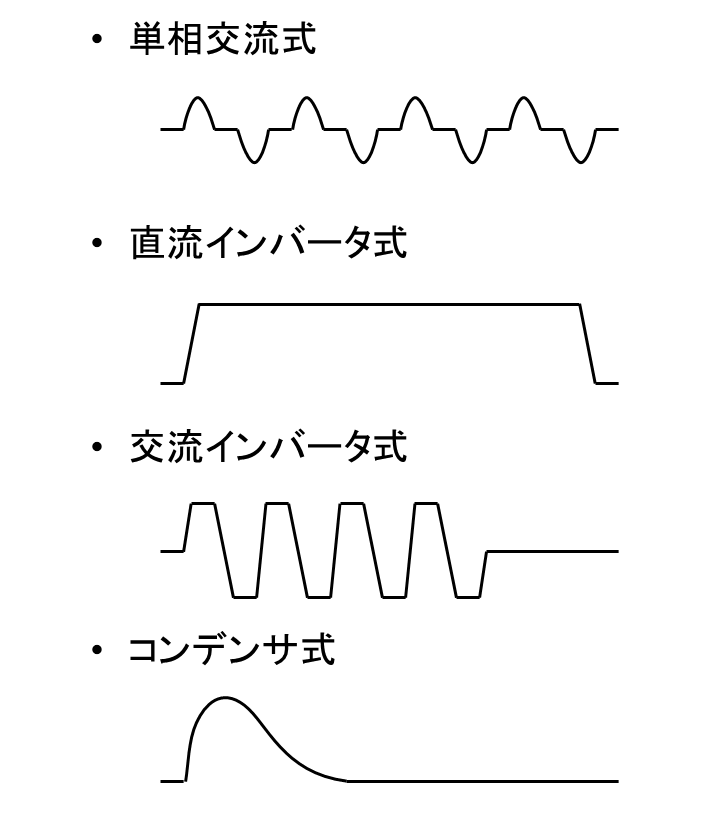
電流波形
関連製品
スポット溶接機とプロジェクション溶接機は何が違うのですか。
スポット溶接機とプロジェクション溶接機の機器構成は同じです。しかし、プロジェクション溶接では電極の平行度が重要になるため、機械の剛性を高めており、加圧時におけるたわみを抑制しています。また、より高い電流値が必要になることが多いため、最大短絡電流も高めに設定されています。
スポット溶接機でも電極の交換と溶接条件の変更により、ナットやボルトのプロジェクション溶接、突き合わせ溶接であるバット溶接なども可能となります。
また、エナメル線に端子を圧着する際に、エナメルを剥がすことなく圧着が出来る通電熱かしめなども可能です。
この様に、被溶接物に求められる溶接品質に合わせて機種を選定します。
関連製品
散りとは何ですか。
散りの現象を指して一般的にスパッタと呼ばれておりますが、正しくは抵抗溶接においては散りと呼ばれ電極と被溶接物の間から発生するものを表散り、被溶接物間から発生するものを中散りと呼びます。
散りは適正溶接条件に対して溶接電流が高い、通電時間が長い、加圧力が低い場合に発生しやすくなります。
溶接電流を下げる、通電時間を短くする、加圧力を上げることや、スポット溶接の場合はアップスロープを入れることで散りを減らすことが出来ます。
プロジェクション溶接の場合には電極の平行度が出ていない場合や、スポット溶接の場合には板隙などの外乱により発生する場合も有ります。
単相交流式の電流制御方法について教えてください。
単相交流式ではサイリスタと呼ばれる半導体を点弧するタイミングを変化させることで溶接電流を制御しています。この制御方法を位相制御と呼びます。
溶接電流が一定になる様にフィードバック制御をすることを定電流制御と呼びます。
また、入力電圧を検知し電圧が一定になる様にフィードバック制御をすることを電圧補償制御と呼びます。
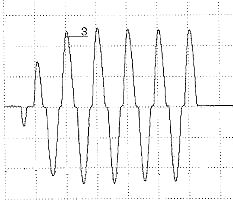
単相交流式の電流波形
直流インバータ式の電流制御方法について教えてください。
交流インバータ式の電流制御方法について教えてください。
コンデンサ式の電流制御方法について教えてください。
コンデンサ式では充電電圧を調整することでエネルギーを調整しています。一般的なコンデンサ式ではサイリスタにより放電するため、充電されたエネルギーは全て放電されます。
弊社のコンデンサ式では充電電圧を調整することでエネルギーを調整しつつ、放電時にはIGBTを使用してインバータ制御しているため、直流インバータ式の様な定電流制御が可能です。また、残ったエネルギーは次の溶接に使用することが出来るため合理的な制御方法であると言えます。
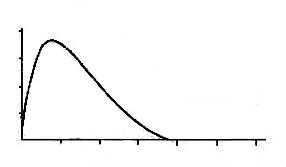
コンデンサ式の電流波形
関連製品
コンデンサ式を使用するメリットは何ですか。
コンデンサ式ではコンデンサに充電したエネルギーを短時間で放電するため、次のようなメリットが有ります。
1.設備容量が小さく、通常の単相交流式などと比べ1/10程度となります。
2.一次電圧が変動する場合でも溶接電流には影響が有りません。
3.溶接部から周囲への熱伝導が少ないため焼けやひずみが出にくくなります。
4.ホットスタンプ(ホットプレス)材へのナット等のプロジェクション溶接において安定した溶接強度が得られます。
5.単相交流式と比べ消費エネルギーが1/3程度と省エネが可能です。(弊社実験による)
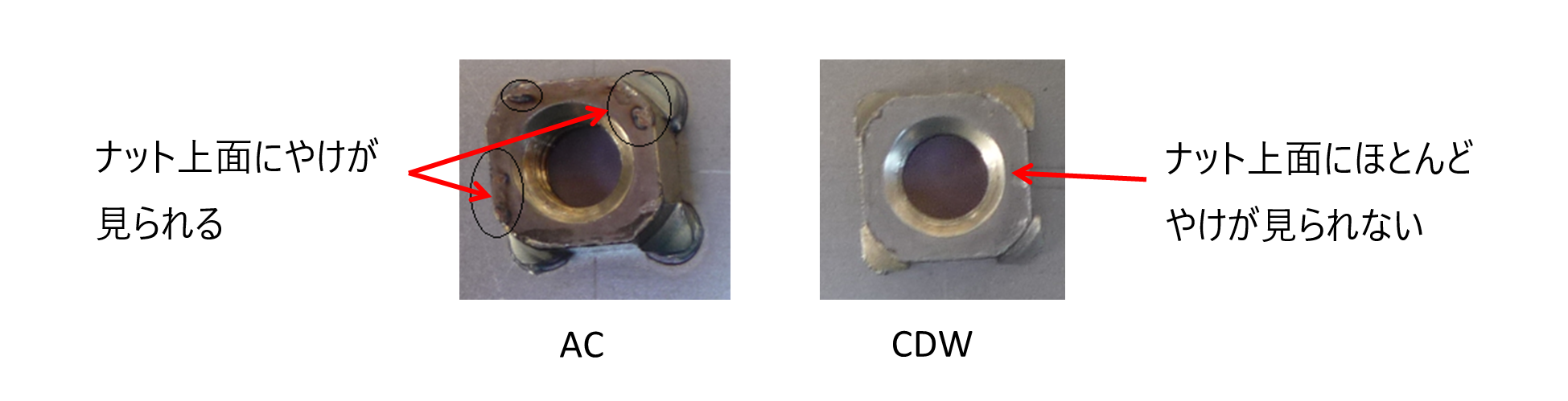
溶接後のナット上面写真
関連製品
古い溶接機を使用しているのですがPCBを含有していますか。
一般社団法人 日本溶接協会では「PCB含有コンデンサー(微量混入が懸念されるものを含む)を使用した溶接機のメーカー名、機器名、型式名及び製造時期」を公開しております。以下のページよりPDFファイルをダウンロードすることが出来ますのでご確認ください。
https://www.jwes.or.jp/committees/electric/notice/
リストにない装置の場合はお手数ですがリンク先の「メーカーお問合せ窓口」より弊社までお問合せ下さい。
フィーダを使用する上で注意する点はありますか。
ナットに油が多量に付着していると振動式フィーダではトラック上をナットが進まなくなる場合が有ります。また、ナットが滑り落ちるシュートレールなどではナットがシュートレールに貼りついてしまい進まなくなることも有ります。油は最小限にとどめることをお勧めします。
送給チューブと呼ばれるナットやボルトをエアブローで飛ばすチューブの取り回しについても注意が必要です。チューブの曲げRが小さいと、ナットやボルトの詰まりが発生したりチューブ内面の異常摩耗が発生し易くなります。チューブについては出来るだけ滑らかに大きなRになる様に設置することが大切です。
関連製品
メサコンとLinearWaveはどう違いますか。
メサコン(Mesa Condenser)は弊社統合前のナストーア溶接テクノロジーで生産していましたが、LinearWaveは会社統合時に商標を登録し名称を変更したものです。どちらもインバータ式コンデンサ溶接機で違いはありません。
ナットフィーダの機種選定方法を教えてください。
アップスロープとは何ですか。
アップスロープとはスポット溶接の際に溶接電流を徐々に上げていくことで、板隙がある場合に合いを良くしたり、散りを出にくくしたりする場合に使用されます。
プロジェクション溶接ではアップスロープを入れると溶接強度が下がる傾向が有りますので、アップスロープを入れない方が良いでしょう。強度は十分であるが散りが問題となっている場合などにはアップスロープを入れる場合も有ります。
必要な品質を満足するように設定することが重要です。
電極の平行度はどのように確認すれば良いですか。
スポット溶接などの場合はある程度の平行度が出ていれば、溶接品質に大きな影響は無いので目視でも構いませんが、プロジェクション溶接の場合には平行度が重要になります。
平行度を確認するには上下電極間に感圧紙などと呼ばれる、圧力がかかると変色するシートを挟んで平行度を確認します。
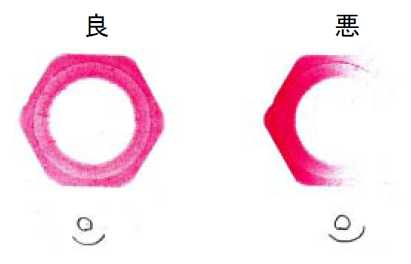
感圧紙による平行度の確認
抵抗溶接をするには資格が必要ですか。
法定の資格などは有りません。
抵抗溶接は初めに適正な溶接条件を設定することで安定した品質が得られる溶接方法です。溶接の際には足踏みスイッチなどで起動するだけなので、技能を求められることはありません。但し、数kN~数十kNという加圧力を発生し、数千A~数万Aという大電流を流せる設備ですので、作業者には安全教育が必要です。
スポット溶接部の検査方法を教えてください。
要求品質に応じた検査方法が求められますが、代表的な物では断面マクロ試験によりナゲット径などを測定する場合や、TSSと呼ばれる引張せん断強さやCTSと呼ばれる十字引張強さを測定する方法が有ります。
これらの測定方法は実際の製品では実施出来ない場合が多く、その場合は現場での試験が容易なたがね試験、ピール試験、ねじり試験を行う場合も有ります。
これらの測定方法はJISにも規定されておりますのでご参考ください。
- JIS Z 3140:スポット溶接部の検査方法及び判定基準
- JIS Z 3144:スポット及びプロジェクション溶接部の現場試験方法
- JIS Z 3139:スポット,プロジェクション及びシーム溶接部の断面試験方法
- JIS Z 3136:抵抗スポット及びプロジェクション溶接継手のせん断試験に対する試験片寸法及び試験方法
- JIS Z 3137:抵抗スポット及びプロジェクション溶接継手の十字引張試験に対する試験片寸法及び試験方法
- JIS Z 3138:スポット溶接継手の疲れ試験方法
溶接機はどのように選定すれば良いですか。
弊社に実際のワークや図面などをご提供していただき、要求品質などをご連絡頂ければ弊社で選定することが可能です。
選定が困難な場合には、弊社の実験設備にて実際に溶接をして選定することも可能です。
溶接電流はどのように測定すれば良いですか。
抵抗溶接では数千~数万Aという電流を流しますので一般的な測定器での測定は困難です。そのため、溶接電流を測定するためには専用の電流計が存在します。
この電流計ではトロイダルコイルを二次側に設置し溶接電流を測定することが出来ます。また、通電時間も併せて測定できます。
加圧力はどのように測定すれば良いですか。
市販のロードセルなどを使用して測定することも出来ますが、専用の加圧力計も存在し、市販のロードセルなどで測定するよりも容易に使用できるようになっています。
ハンディ溶接計測器WS-100ではオプションのロードセルを接続することで加圧力を測定することもできます。
関連製品
ナストーア株式会社の抵抗溶接機のサポートは行っていますか?
はい、行っております。
ナストーアに限らず、東亜精機、ナストーア溶接テクノロジー、電元社製作所等、旧社名の抵抗溶接機全般のサポートが可能ですのでお気軽にお問い合わせください。
なお、アーク溶接機のサポートは行っておりません。
関連製品
冷却水はどのように供給すれば良いですか。
工場にクーリングタワー(冷却塔)が有れば良いのですが、無い場合には市販のチラーユニットや弊社製の水冷装置を使用することをお勧めします。使用上は水道水でも問題はありませんが、水道料金を考慮するとお勧め出来ません。
チラーユニットを使用する場合は結露に注意が必要です。
関連製品
パイロット通電とは何ですか。
ナット溶接などのプロジェクション溶接では、通電初期の1~2サイクル程度で溶接強度が決まってしまいます。通電初期の電流が低く突起が十分に加熱される前に突起が潰れてしまうと溶接強度が低くなります。パイロット通電機能では通電初期の電流を適切に設定することが出来、溶接品質を向上することが出来ます。
抵抗溶接の品質管理方法を教えてください。
スポット溶接を連続で行うと、電極先端が摩耗し、徐々に被溶接物との接触径が大きくなります。スポット溶接は前述の通り電極先端径を小さくし、溶接する部分の電流密度を維持する必要があるため、あらかじめチップドレス周期を決めて管理します。電極は市販されているドレッサや旋盤などでチップドレスをおこないます。
更に、最近では通信機能を備え溶接結果をPCに送信できる制御装置やドレスの良否判定が出来る制御装置も販売されていますので、最新の装置を導入することで、より確実な品質管理が可能になります。
プロジェクション溶接の場合、電極と被溶接物との接触面や上下電極の平行度が重要となり溶接品質に影響します。旋盤やフライス盤などで電極を整形します。また、プロジェクション溶接では溶接電流の立ち上がりが溶接品質に大きく影響しますので、電流の立ち上がりをより繊細に制御できる制御装置も販売されています。
シーム溶接の場合は、一般的には整形バイトが付属しておりますので、それを使用します。
関連製品
アルミニウム合金のスポット溶接は可能ですか。
可能です。
アルミニウム合金の場合は鋼板に比べて材料の固有抵抗が低いため、大電流が必要になります。
また、表面に酸化被膜があるため、溶接品質を安定させるためにはステンレス製のワイヤブラシなどで酸化被膜を除去する必要があります。
溶接部の断面を観察した際に、ブローホールと呼ばれる空孔がナゲット内部に見られることがあります。ブローホールは通電の後半から電極加圧力を高くする鍛圧や急冷を防ぐための後熱電流により少なくすることが出来ます。
最近では溶接電流と電極加圧力を同期して制御できるロボット及び溶接制御装置が販売されています。
尚、電極面にはアルミニウムが付着し、それが溶接品質のバラツキや、溶接痕が汚くなる原因となるので頻繁にチップドレスする必要があります。
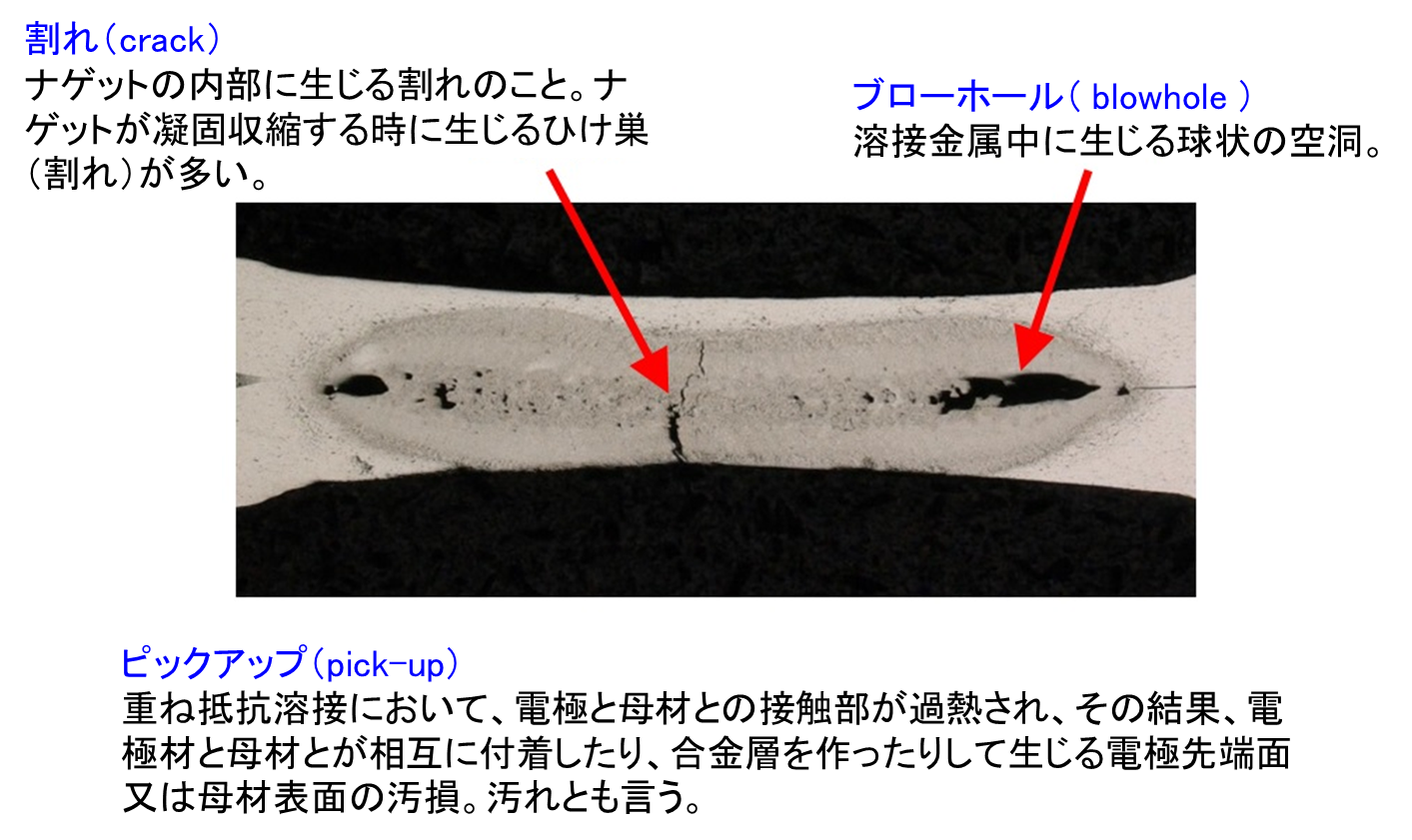
マクロ試験断面写真
関連製品
ワークの形状により通常のスポット溶接機が使用できません。
ワークの形状に合わせた電極をご用意できます。弊社ではオフセット電極もご用意しておりますのでご相談ください。
また、ワーク図やCADデータなどを提供いただければ、適切な電極を設計製作することも可能です。
スポット溶接をしたら割れが出てしまいます。
炭素鋼などをスポット溶接すると溶接部に焼きが入ってしまい、もろくなる場合が有ります。そのような場合には,マルテンパーやオーステンパーと呼ばれる後熱電流を流すことで硬度を下げることが出来ます。硬度を下げることで割れが発生しにくくなります。
プロジェクション溶接で強度が不足します。
炭素が多く含まれた材料では溶接部に焼きが入ってしまい、母材破断しても溶接強度が不足する場合が有ります。
そのような場合にはマルテンパーやオーステンパーと呼ばれる後熱電流を流すことで硬度を下げることが出来ます。硬度を下げることで接合部に応力が集中しにくくなり溶接強度を上げられる場合が有ります。
関連製品
薄板と厚板をスポット溶接出来ますか。
薄板と厚板のスポット溶接では接合面より厚板側にナゲットが寄る傾向が見られます。
一般的には板厚比が1:3程度までであれば薄板側の溶接条件で溶接出来ますが、ナゲットが接合面まで広がっていない場合には電流を高くしたり、薄板側の電極の先端径を細くするか先端Rを小さくしたりすることでナゲットが薄板側に寄ります。
断面マクロ試験で使用する腐食液を教えてください。
鋼板の場合には、一般的にナイタール液やピクリン酸溶液を使用します。
SUS材の場合には、一般的にシュウ酸溶液を使用し電解エッチングします。
アルミニウム合金の場合には、一般的にケラー試薬を使用します。
溶接ナットにはどのような種類が有りますか。
溶接ナットはJIS B 1196で規定されており、形状として六角溶接ナット、四角溶接ナット、T形溶接ナットが規定されております。
その他にも丸ナットやフランジ付きのナットが使用されておりますが、入手性や経済性の面では四角ナットが優れております。
溶接ナットのパイロットは何のために有りますか。
パネルとナットの位置決めの為にパイロットが有りますが、現在ではガイドピンと呼ばれる絶縁された位置決めピンが組み込まれた電極を使用するため、パイロットが無くても大きな位置ずれは発生しません。溶接性の面ではパイロットが有るとパイロットからパネルに電流が流れてしまい、その分流の程度により溶接強度のばらつきが大きくなってしまいます。
また、ナットフィーダとしては繊細な調整が必要になるため、調整不良による選別ミスなどが発生しやすくなります。これらの事から弊社では特別な事情が無い限りパイロット無しをお勧めいたします。
複数の溶接機にまとめて溶接条件を入力できますか。
溶接結果の履歴を残すことは出来ますか。
弊社では、Wel Net 3Mというソフトウェアを販売しております。Ethernet通信が可能な溶接機、溶接電源でしたら電流値、通電時間、加圧力等の数値だけでなく電流波形や抵抗波形をデータベースに保存することも出来ます。
関連製品
国内の周波数が違う地域に溶接機を移設できますか。
単相交流式の場合は、周波数により巻数比を変更しておりますので改造が必要です。インバータ式の場合はそのまま使用できますが、設定変更が必要な場合もございます。
国内の溶接設備を海外で使用できますか。
米国ではUL規格、欧州ではCEマーキング等の規格が有ります。そのため、電源電圧や周波数が同じでもそのまま使用することは出来ません。弊社では仕向け地の規格に合わせた設備をご用意しておりますので、お気軽にご相談ください。
樹脂と金属を接合出来ますか。
通常のスポット溶接機などでは、樹脂に電流を流せませんので接合出来ません。
弊社では金属側だけに電流を流せるようになっているコアキシャルシリーズスポット溶接機をご用意しております。
抵抗溶接はどのような製品作りに使われていますか。
数多く使われているのは自動車の車体組立ですが、鉄道車両の組立、航空機部品の組立にも使用されています。その他にも側溝の蓋(グレーチング)、道路標識、フェンス、電気自動車に使われるモータの端子、プレハブ住宅、エアコン・冷蔵庫などの家電製品、スチール家具、ドラム缶など身近な製品作りにも使用されています。
点弧、点弧角、通電角とは何ですか。
点 弧:サイリスタをONにさせ、電気を流すことです。
点弧角:サイリスタがONにした時の位相を、角度で表したものです。
通電角:サイリスタの流れた電気の位相を角度で表したものです。最大時(フルウエーブ)通電角180°に対して、何度通電したかを表しています。
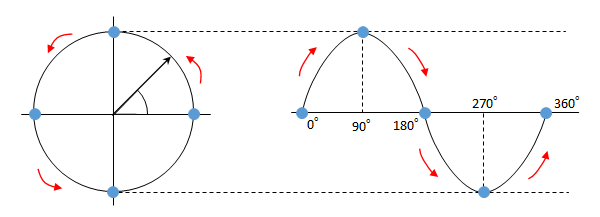
単相電源の波形
CONTACT
総合接合機メーカーとして、お客様の多様なニーズに最適な形でお応えします。