Product
Control device for resistance welding machines
Single phase AC for stand-alone spot welding machine and seam welding machines
Series Features
-
01
Wide range of capacity variations
-
02
Various functions to meet customer needs
-
03
Control of welding conditions by EtherNet communication and traceability of welding result monitor
-
04
Automation-compatible I/Os and reduced wiring
Series Product Details
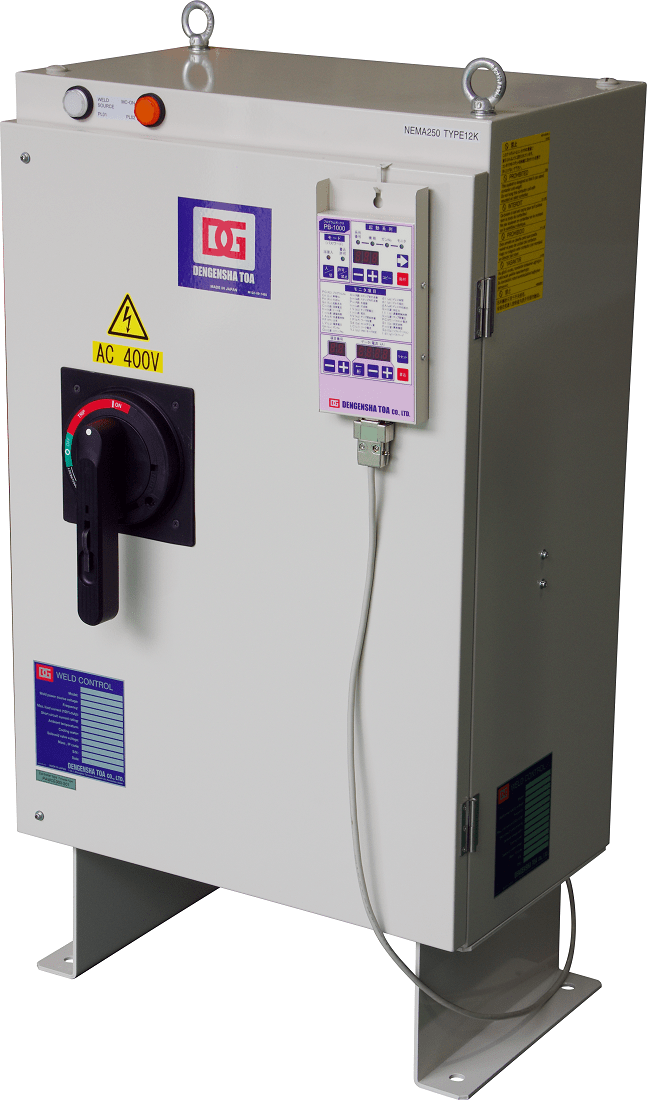
Features
- 255 welding conditions for automation
- Five-stage current passing specifications
- Control of welding conditions by EtherNet communication and traceability of welding result monitor
- High-quality welding of nuts and bolts to high-tensile steel by pilot current
- Pilot current individually monitored, error detected
- Equipped with a current control mode (HCCL) that is compatible with insulating coatings such as mill scale
- Conditions can be changed remotely with the PB specification
- I/O connectivity power Source can be changed to NPN/PNP
- CE compliant
Options
Communication board | Enables Ethernet and EtherNet/IP communications |
PC application software | Conditions can be set and monitored on a PC |
Specification table
Model | Equivalent output current (A) | Specification-wise | Cooling system |
---|---|---|---|
DS-950-E15I-※ | 150 | Robot Specifications | Water cooling |
DS-950-E15A-※ | 150 | Robot Specifications | Air cooling |
DS-950-E25I-※ | 200 | Robot Specifications | Water cooling |
DS-950-E25A-※ | 200 | Robot Specifications | Air cooling |
DS-950-E255I-※ | 250 | Robot Specifications | Water cooling |
DS-950-E45I-※ | 450 | Robot Specifications | Water cooling |
DS-951-5I-※ | – | – | Water cooling |
RWC-955R-※ | – | Timer Single unit | Natural air cooling |
Related products and combined products
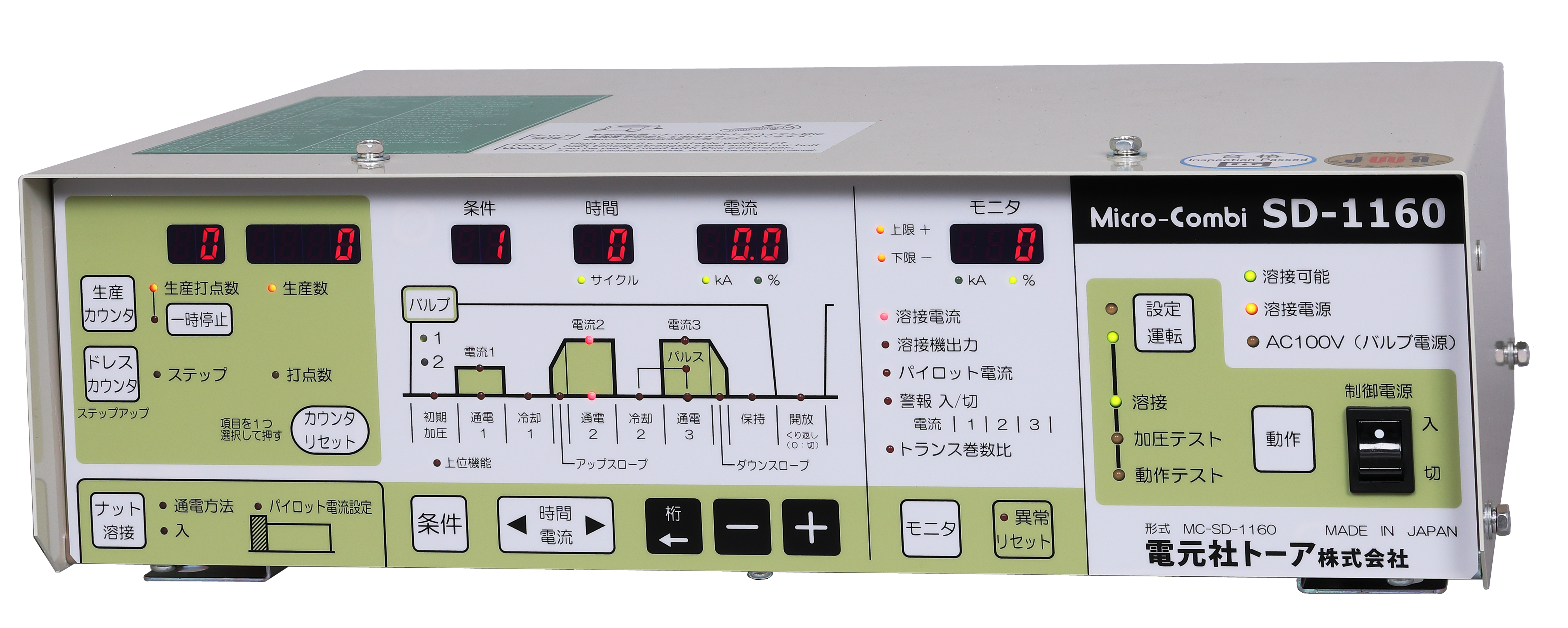
Features
- 60 Welding conditions
- Easy-to-operate panel settings
- Easy pilot current setting with the "Nut mode" panel key
- High-quality welding of nuts and bolts to high-tensile steel by pilot current
- Pilot current individually monitored, error detected
- Electrode pressure directives are available
- Abundant startup input method (binary, BCD)
Options
Electro-pneumatic proportional valve amplifier | Sets electrode force for each welding condition |
Specification table
Model | Contactor | Applications |
---|---|---|
MC-SD-1160 | TC-5C | Spot |
SM-SD-1160 | TC-6C | Seam |
Related products and combined products
Series Features
-
01
High-quality weld with MFDC to suppress scattering
-
02
Voltage Flicker Suppressed by Three-Phase Parallel Input
-
03
Stable by welding plated steel sheets and aluminum alloys
-
04
Abundant capacity
-
05
Various functions to meet customer needs
-
06
Control of welding conditions by EtherNet communication and traceability of welding result monitor
-
07
Automation-compatible I/Os and reduced wiring
-
08
CE compliant
Series Options
Program box | Box for setting welding conditions and monitoring |
Monitor box | Dedicated monitor box |
PC application software | Conditions can be set and monitored on a PC |
Communications cables | Cable for communication connection |
Series Product Details
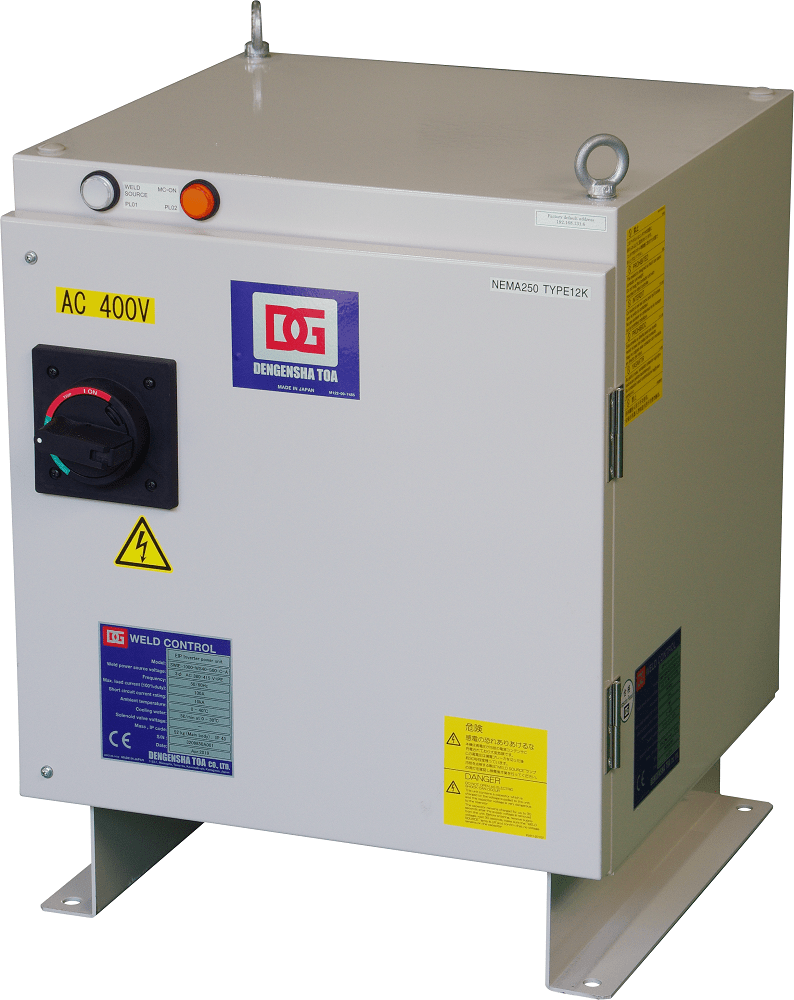
Features
- 255 welding conditions for automation
- Easy set-up with robotics with EtherNet/IP spec. and reduced wiring
- Five-stage current passing specifications
- Control of welding conditions by EtherNet communication and traceability of welding result monitor
- Waveform data such as welding current, voltage between tips, and resistance between tips can be obtained
- Conditions can be managed on the Web
- Dot duty cycle monitor protects transdiode damage
- Chip dress pass/fail judgment function
- Output 400A/300A spec. can be stacked (up to 3 stages)
- I/O power Source can be connected via NPN/PNP
- Supports FANUC pressure profile control function
- CE compliant
Options
Electrode force monitoring (sensor required) | Monitor electrode force during welding |
Secondary Current Sensing Toroidal Coil | Current control with secondary feedback |
Adding a Communication Board | Set two IP addresses (for I/O and data) |
Primary cable degradation detection function (special box required) | Detecting degradation between control device and welding transformer |
Specification table
Model | Rated supply voltage (V) | Output current (A) | Applications | Cooling system |
---|---|---|---|---|
SWIE-1000-WS40 | 380-480 | 400 | Spot | Water cooling |
SWIE-1000-KA30 | 380-480 | 300 | Spot | Air cooling |
SWIE-1000-WS80 | 380-480 | 800 | Spot | Water cooling |
SWIE-1000-WS100 | 380-480 | 1,000 | Spot/Seam | Water cooling |
SWIE-1000-WS200 | 380-480 | 2,000 | Spot/Seam | Water cooling |
Related products and combined products
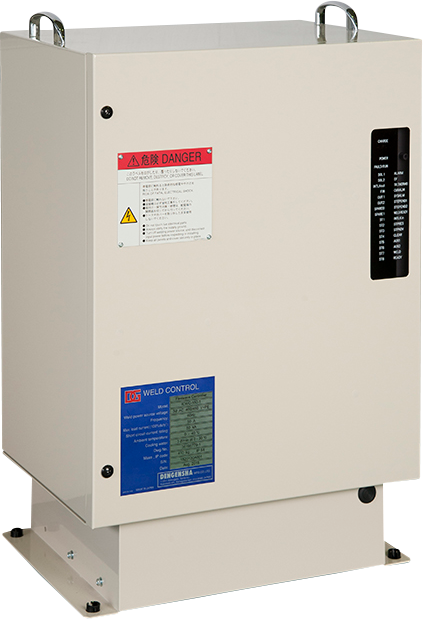
Features
- 255 welding conditions for automation
- Four-stage current passing and strong/weak pulse are possible
- 5-stage electrode pressurization command available (initial pressurization, current 1, current 2&3, current 4, held)
- Abundant startup input method (binary, BCD)
- I/O power Source can be connected via NPN/PNP
- Control device can be connected in parallel to accommodate larger capacities
Options
Electro-pneumatic proportional valve amplifier | Sets electrode force for each welding condition |
Secondary Current Sensing Toroidal Coil | Current control with secondary feedback |
Specification table
Model | Rated capacity (kVA) | Rated supply voltage (V) | Output current (A) | Applications |
---|---|---|---|---|
DIT-723-5 | 75 | 200-220 | 700 | Spot |
DIT-1123-5 | 118 | 200-220 | 1,100 | Spot |
DIT-543-5 | 108 | 400-440 | 500 | Spot |
DIT-843-5 | 173 | 400-440 | 800 | Spot |
DIT-1043-5 | 216 | 400-440 | 1,000 | Spot |
DIT-1643-5 | 346 | 400-440 | 1,600 | Spot |
DIT-825-5 | 214 | 200-220 | 800 | Seam |
DIT-845-5 | 429 | 400-440 | 800 | Seam |
Related products and combined products
Series Features
-
01
Single-phase AC welding machines can be transformed into inverters simply by replacing control device
-
02
High-quality welding with AC inverter to suppress scattering
-
03
Effective in suppressing voltage flicker
-
04
Enables faster seam welding
-
05
Abundant capacity
-
06
Various functions to meet customer needs
-
07
Control of welding conditions by EtherNet communication and traceability of welding result monitor
-
08
Automation-compatible I/Os and reduced wiring
Series Options
Program box | Box for setting welding conditions and monitoring |
Monitor box | Dedicated monitor box |
PC application software | Conditions can be set and monitored on a PC |
Communications cables | Cable for communication connection |
Series Product Details
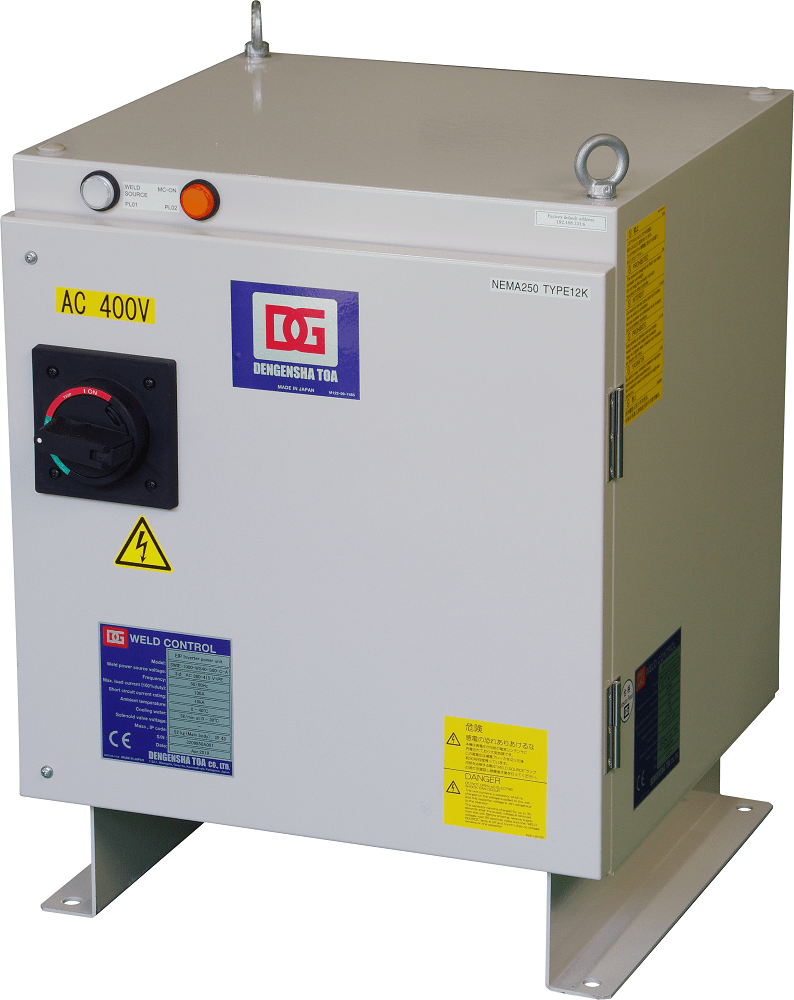
Features
- 255 welding conditions for automation
- Easy set-up with robotics with EtherNet/IP spec. and reduced wiring
- Five-stage current passing specifications
- Control of welding conditions by EtherNet communication and traceability of welding result monitor
- Conditions can be managed on the Web
- CE compliant
Options
Electrode force monitoring (sensor required) | Monitor electrode force during welding |
Secondary Current Sensing Toroidal Coil | Current control with secondary feedback |
Adding a Communication Board | Set two IP addresses (for I/O and data) |
Specification table
Model | Rated supply voltage (V) | Output current (A) | Applications | Cooling system |
---|---|---|---|---|
SWIE-1050-WS40 | 380-480 | 400 | Spot | Water cooling |
SWIE-1050-KA30 | 380-480 | 300 | Spot | Air cooling |
SWIE-1050-WS80 | 380-480 | 800 | Spot | Water cooling |
SWIE-1050-WS100 | 380-480 | 1,000 | Spot/Seam | Water cooling |
SWIE-1050-WS200 | 380-480 | 2,000 | Spot/Seam | Water cooling |
Related products and combined products
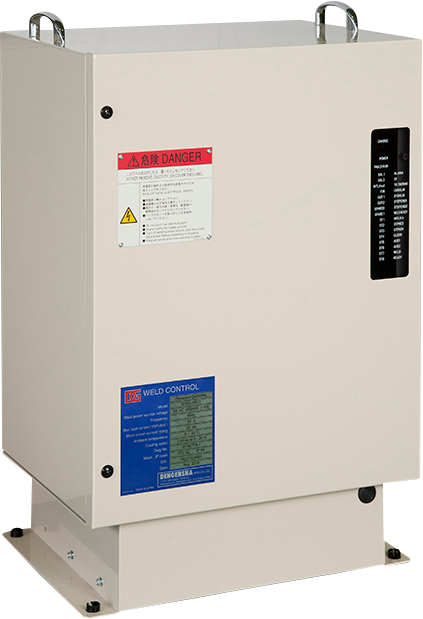
Features
- 255 welding conditions for automation
- Four-stage current passing strong/weak pulse power supply are possible
- 5-stage electrode pressurization command available (initial pressurization, current 1, current 2&3, current 4, held)
- Abundant startup input method (binary, BCD)
- I/O power Source can be connected via NPN/PNP
- Control device can be connected in parallel to accommodate larger capacities
Options
Electro-pneumatic proportional valve amplifier | Sets electrode force for each welding condition |
Secondary Current Sensing Toroidal Coil | Current control with secondary feedback |
Specification table
Model | Rated capacity (kVA) | Rated supply voltage (V) | Output current (A) | Applications |
---|---|---|---|---|
AIT-724-5 | 75 | 200-220 | 700 | Spot |
AIT-1124-5 | 118 | 200-220 | 1,100 | Spot |
AIT-544-5 | 108 | 400-440 | 500 | Spot |
AIT-844-5 | 173 | 400-440 | 800 | Spot |
AIT-1044-5 | 216 | 400-440 | 1,000 | Spot |
AIT-1644-5 | 346 | 400-440 | 1,600 | Spot |
AIT-826-5 | 214 | 200-220 | 800 | Seam |
AIT-846-5 | 429 | 400-440 | 800 | Seam |
Related products and combined products
Series Features
-
01
Mount timer board on the robotic control panel and set up easily
-
02
Cycle time can be shortened by commanding drectly to the robot by dual port RAM
-
03
No need for control wiring with the robot
-
04
Welding conditions and monitoring operation are possible with the robot's teach pendant
-
05
Can be stacked (up to three stages)
-
06
255 Welding Conditions
-
07
Five-stage current passing specifications
-
08
Contactor is compatible with air-cooled 300A/ water-cooled 400A
-
09
Equipped with breaker and output magnet as standard
-
10
CE compliant
Series Product Details
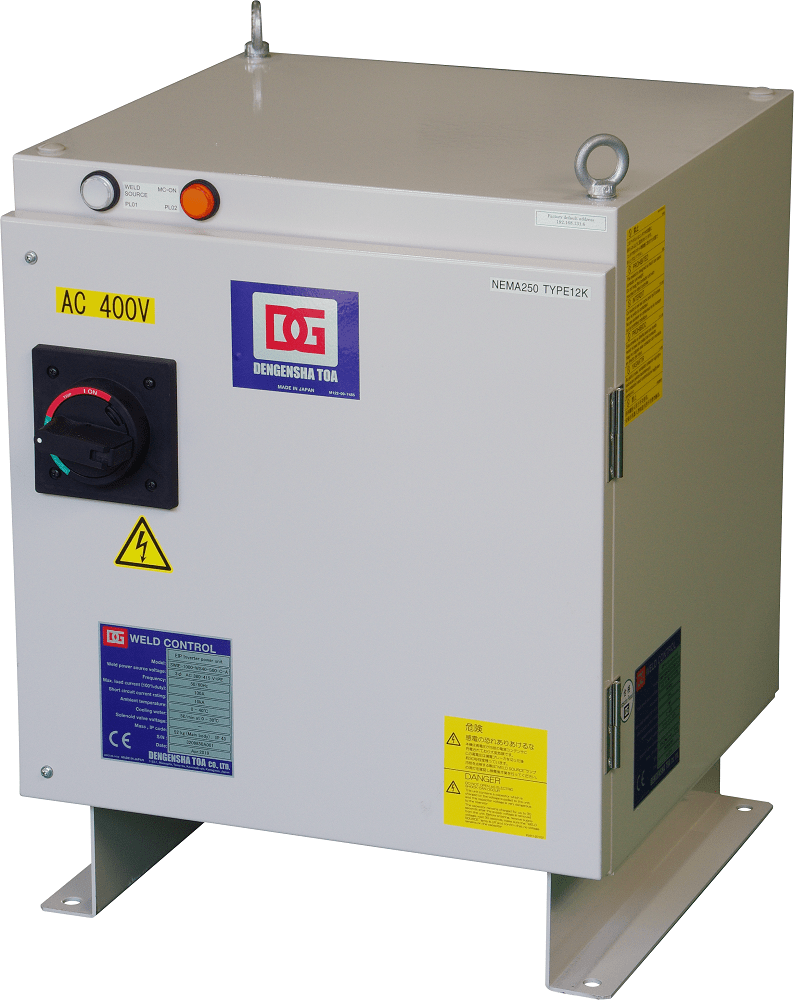
Features
- Dot duty cycle monitor protects transdiode damage
Options
EtherNet communication board | Management of welding conditions and traceability of welding result monitor |
Sensing wire for voltage between tips | For monitoring welding voltage |
Obtain waveform of current and resistance between tips | Waveform data output every 0.5 cycles |
PC application software | Conditions can be set and monitored on a PC |
Compatible with FANUC ZDT (zero down time) | Supports the server management system for monitor data |
Specification table
Model | Robot | Robot control panel | Control method |
---|---|---|---|
RWC2000 | FANUC | R-J3i, R-30i/plus (PC104) | Single-phase ac |
RWI2100 | FANUC | R-J3i, R-30i/plus (PC104) | DC inverter |
Related products and combined products
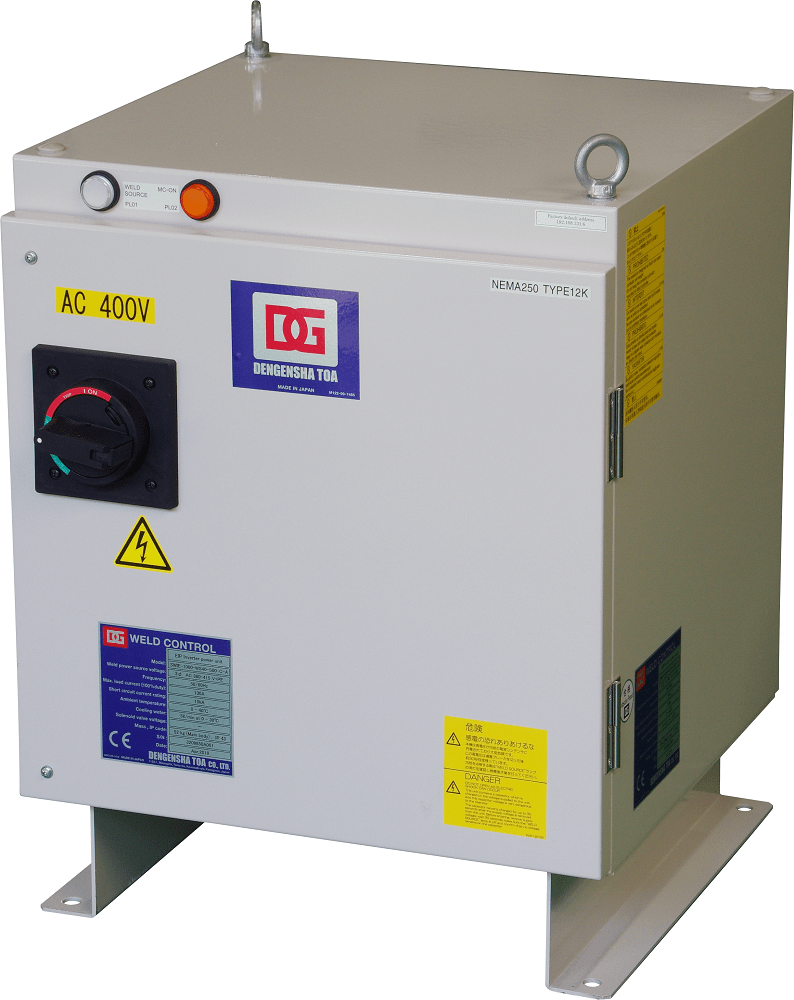
Features
- Leak check function
- Supports NACHI electrode force control (changeable pressure during welding)
Specification table
Model | Robot | Robot control panel | Control method |
---|---|---|---|
RWC3200 | NACHI | NACHI AX, FD controller (PCI) | Single-phase AC |
RWI3200 | NACHI | NACHI AX, FD controller (PCI) | DC inverter |
RWC4200 | YASKAWA | YASKAWA NX100, DX100, DX200, YRC1000 (PCI) | Single-phase AC |
RWI4200 | YASKAWA | YASKAWA NX100, DX100, DX200, YRC1000 (PCI) | DC inverter |
RWC5200 | KAWASAKI | KAWASAKI E controller, Universal controller (PCI) | Single-phase AC |
RWI5200 | KAWASAKI | KAWASAKI E controller, Universal controller (PCI) | DC inverter |
Related products and combined products
Series Features
-
01
Up to 100 networked timers with EtherNet communication
-
02
Welding conditions can be controlled
-
03
Traceability of welding results
-
04
Monitor timer error data
-
05
Monitor welding current wave and resistance between tips
-
06
Graphical display of waveform data
Series Product Details
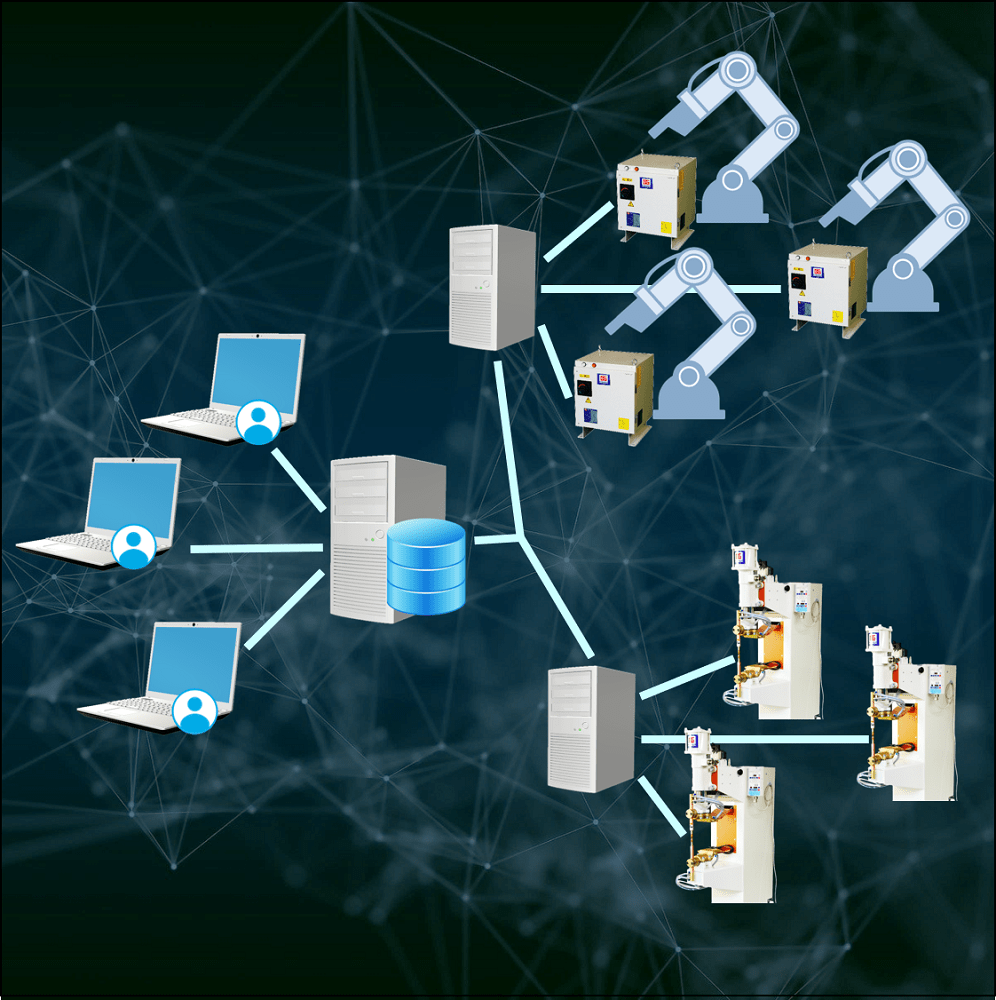
Features
- Screen configuration that can be seen at a glance
- Easy-to-operate screen configuration
- Transfer master data of welding conditions to multiple units
- Monitor abnormal production status with line operation monitor
- Tracking the history of anomalies
Related products and combined products
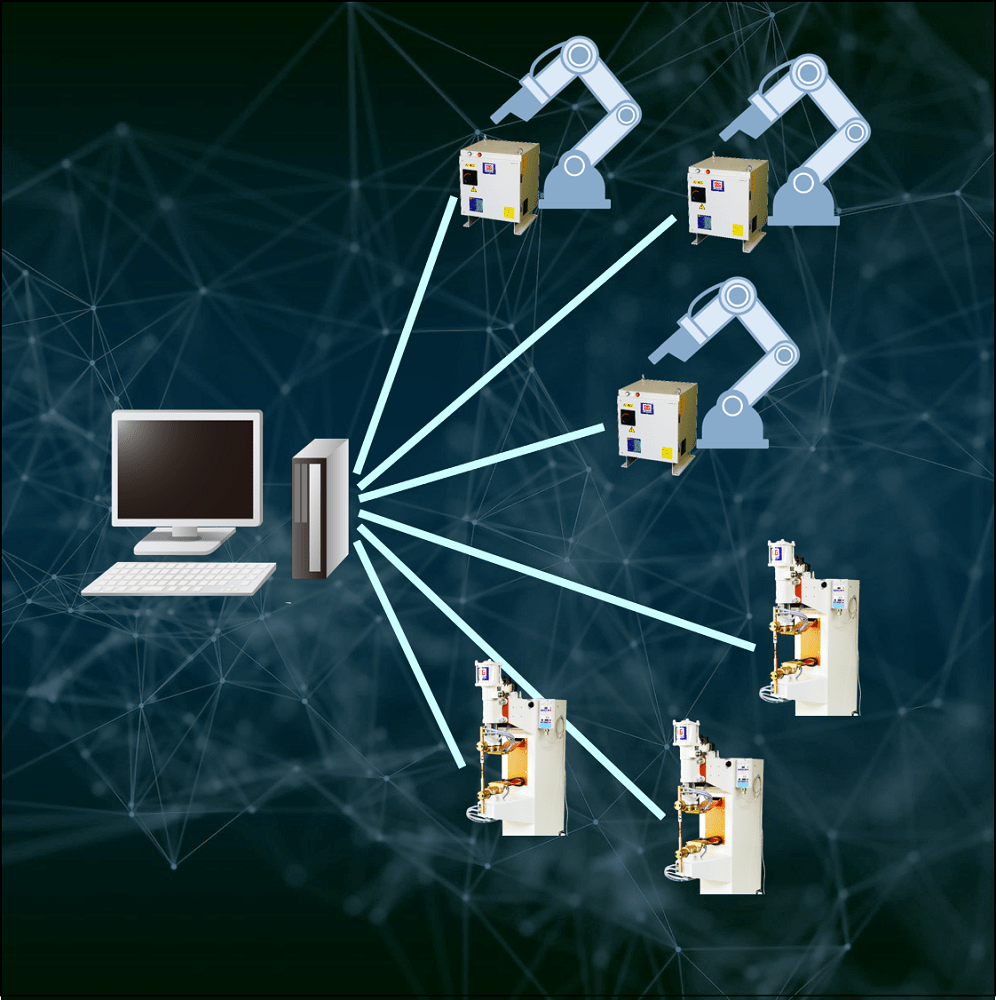
Features
- Control of welding conditions
- Monitoring Various timer information
- Graphical display of waveform data
Related products and combined products
CONTACT
As a full-line joining machine manufacturer, we provide optimal solutions to the diverse needs of our customers.