Solutions
Realizing coolant-free welding machines
Decarbonization Solution
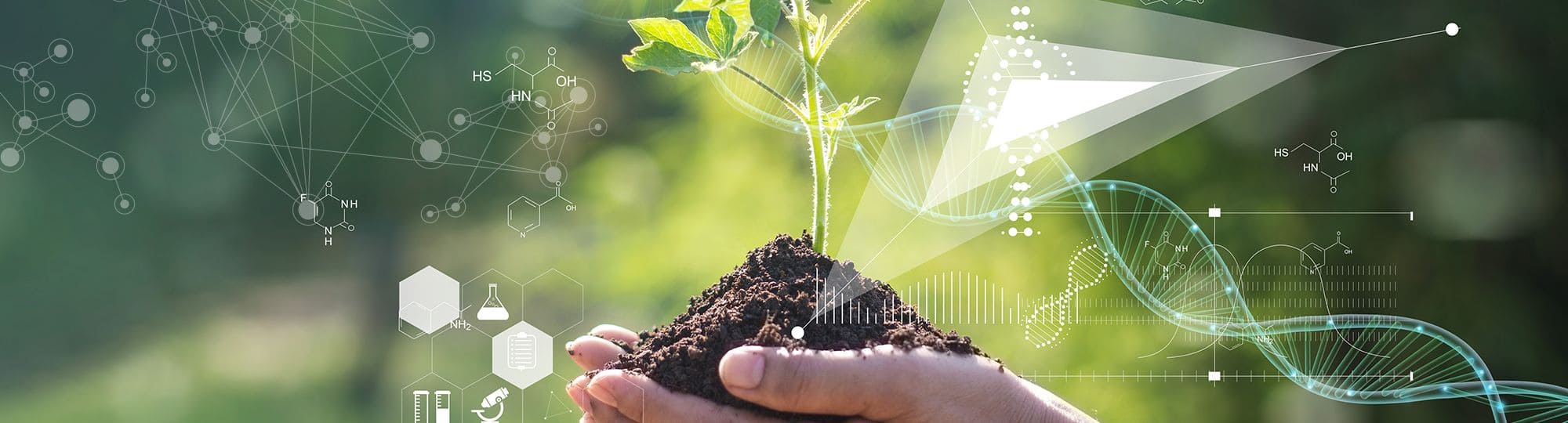

Realizing carbon neutrality
The Japanese government declared that it would aim for carbon neutrality, which would reduce greenhouse gas emissions as a whole to zero by 2050.
Low-power products are also required for factory equipment to achieve carbon neutrality.
Current status of the vehicle body assembly process
A large number of spot-welding machines and parts feeders are used for projection welding of weld nuts and weld bolts on steel plates during the vehicle body assembly process.
Because this projection welding equipment requires a large current, we can say it is a type of equipment that requires a relatively large power consumption.
In addition, as cooling water is normally required for projection welding machines, the power consumption in chillers and cooling towers should not be overlooked either.

DENGENSHA TOA Solutions
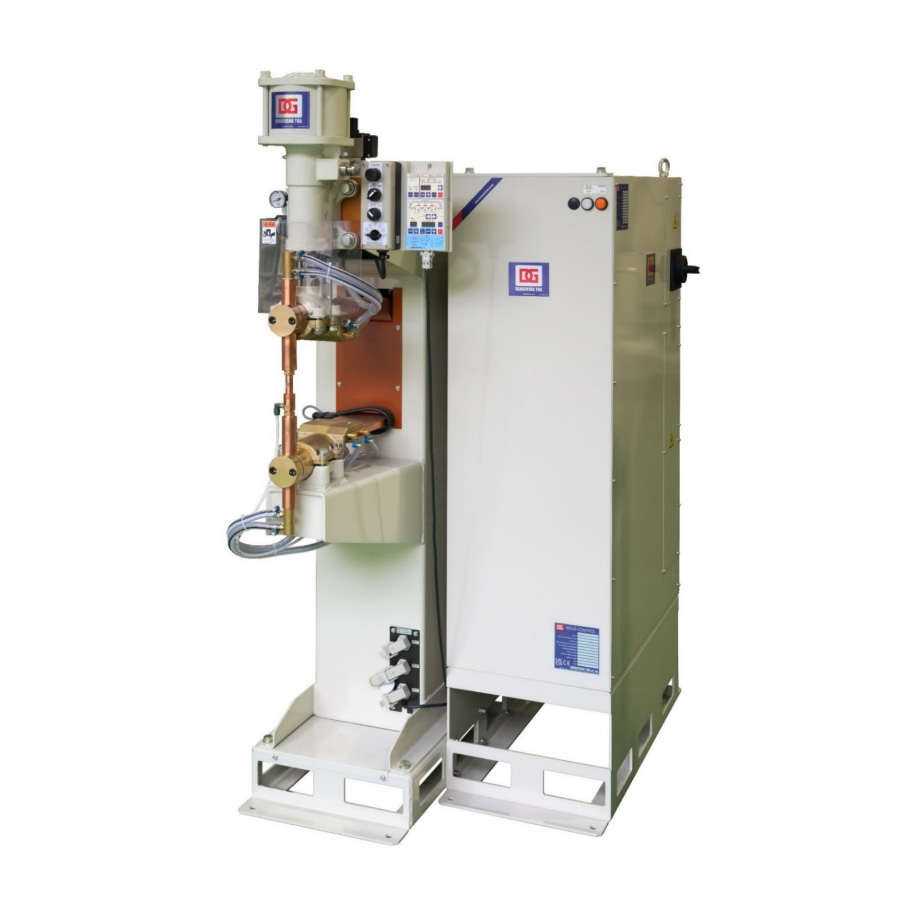
Water-cooling-less capacitor type NDZ
(stationary spot welding machine)
Conventional resistance welding machines require cooling water to cool transformers, thyristors and electrodes.Water-cooling-less capacitor type NDZ utilizes low heat, characterized by the capacitor welder’s short burst of high weld current, as well as the exhaust air that would otherwise be disposed of in the atmosphere.
This saves 1,728 kWh of electricity per year (our estimate) compared to a water-cooling type using a chiller.This translates into an annual reduction of 1,014 kg of CO2 emissions.
In addition to this, the air-cooled welder has many other advantages, such as no condensation even in humid conditions, no water leakage when changing electrodes, and no chiller maintenance.
Additionally, general advantages of capacitor-type welding machines include the ability to reduce power consumption during welding to anywhere from one-half to one-third compared to single-phase AC and DC inverter welding machines, the ability to weld with less thermal strain, and the ability to improve welding quality.
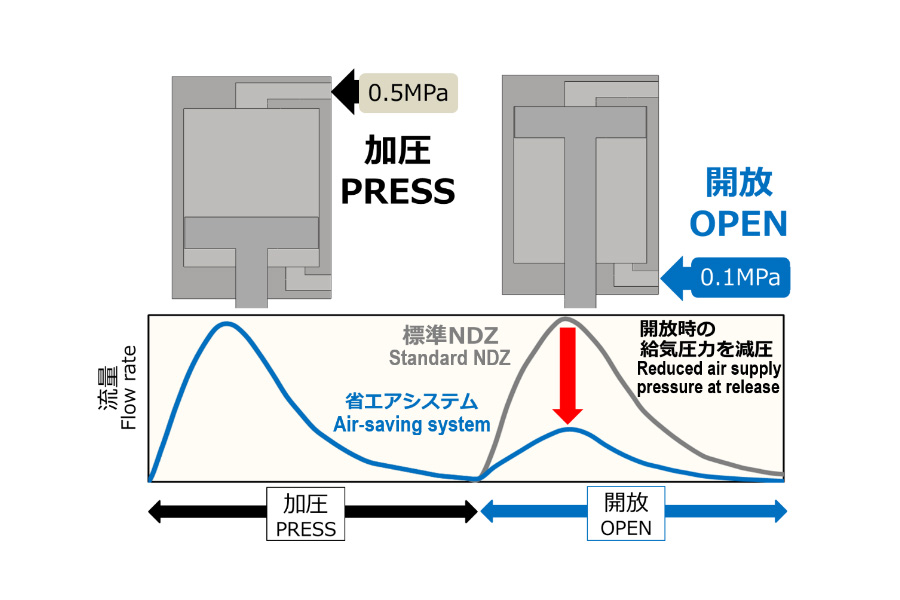
NDZ air-saving system
Reduced air supply pressure on the open end of the pressure unit allows reduction of air consumption. Air consumption can be reduced by up to 38%, which translates into a reduction of 461 kg (our estimate) of annual CO2 emissions.
Simply adding a pressure reducing valve on the open side would result in an extremely slow opening speed; however, with optimal selections of air equipment and parameters, our approach has been successful without notably extending the cycle time.
(*Note: Not applicable to water-cooled capacitor-type NDZ)
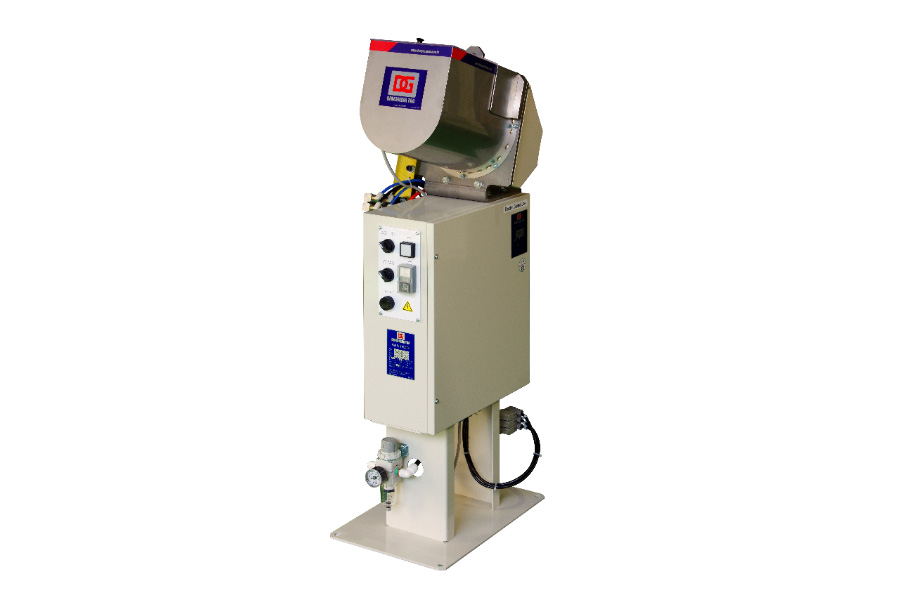
Compact feeder
The conventional vibratory feeder has a large vibrating bowl, which consumes around 100-200 W of electricity during vibration. In contract, the compact feeder uses a motor to simply rotate a small rotating plate, which consumes less than 40W even during rotation, achieving a lower electric consumption level.
DENGENSHA TOA will continue to contribute to society through the development of products that support carbon neutrality.
Related products and combined products
CONTACT
As a full-line joining machine manufacturer, we provide optimal solutions to the diverse needs of our customers.