Solutions
Innovation of welding control operations
DX Solution


Quality control in resistance welding
Resistance welding is a highly reproducible welding method if the four major welding parameters – welding current, weld time, electrode force, and electrode shape – are managed and maintained.Therefore, managing weld parameters and keeping traceability of changes are important control items.
Challenges in quality control
In conventional resistance welders, welding parameters typically are set individually using a panel or a program box of the controller.In addition, information such as monitor data and error history are only displayed or retained on individual devices.
Therefore, the administrator would have to physically go to the place where the welding machine is installed and input parameters or check the error history.

DENGENSHA TOA Solutions
Visualization and centralized management
DENGENSHA TOA has developed a software called Wel Net 3M for centralized control and has added a communication function to the controller to enable centralized control of welding parameters and collection of monitor data.
This enables the administrator to set the welding parameters and check the monitored data from anywhere on the network at any time.
If a welding failure occurs, this will allow you not only to check the abnormal log or the monitored numerical welding current, but also to check the history of the current waveform and the resistance waveform.
In addition, the pressure can be monitored numerically by connecting a sensor to the controller that can measure the pressure.
The controller also provides a tip-dress judgment function, which can be used together with these functions keeping a history of all four major welding parameters – welding current, weld time, electrode force, and electrode shape. These features will help to enhance quality control and innovate control operations.
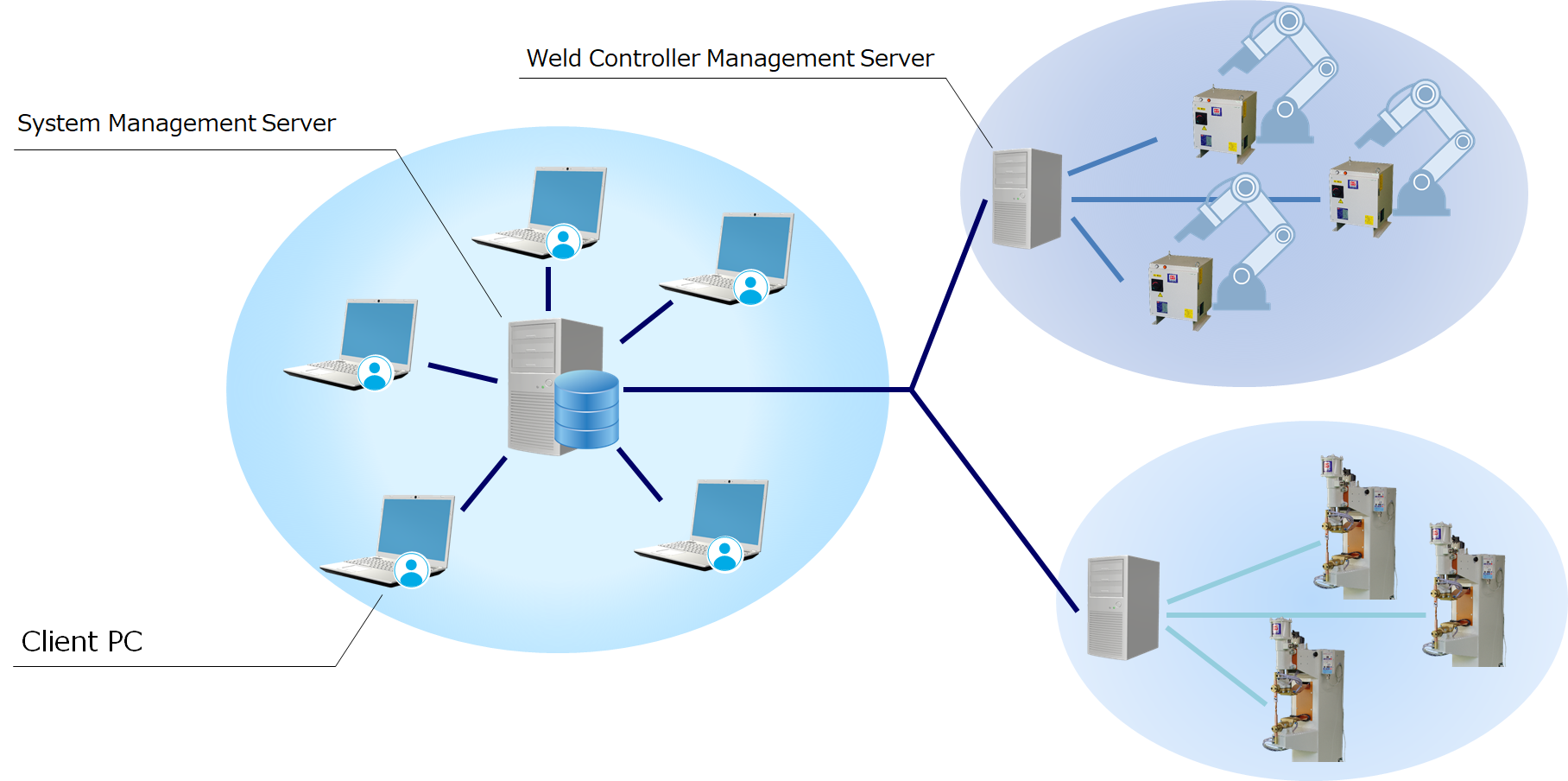
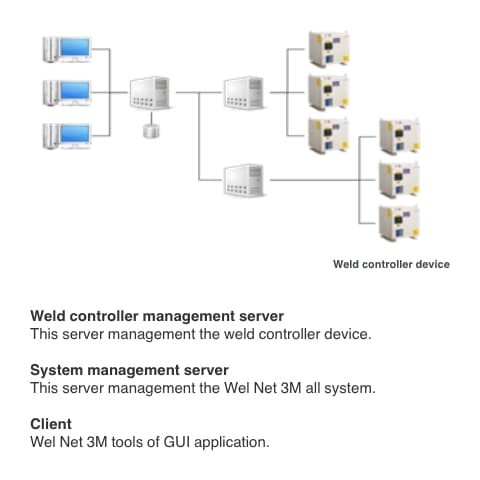
Related Products
CONTACT
As a full-line joining machine manufacturer, we provide optimal solutions to the diverse needs of our customers.